China-based one-stop manufacturer of medical products
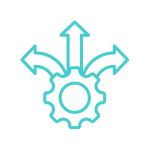
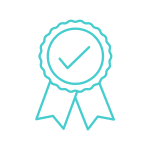

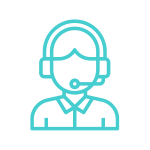
We are a Chinese manufacturer of medical products.
-
Our product range includes three essential types of disposable protective garments, each engineered to deliver targeted protection for diverse professional environments:
- Disposable Isolation Gowns
These gowns are designed for use in healthcare settings, laboratories, and cleanrooms to create a physical barrier between the wearer and potential contaminants. Crafted from lightweight, fluid-resistant non-woven fabric, they feature full-length coverage, extending from the neck to the knees, with long sleeves and elastic cuffs to seal around the wrists. Equipped with a secure tie-back closure at the waist, they ensure a snug fit while allowing ease of movement. Their primary function is to protect wearers from contact with infectious materials, bodily fluids, or hazardous substances, as well as to prevent the transfer of contaminants from the wearer to patients or work surfaces. They are ideal for low to moderate risk scenarios, such as patient care, specimen handling, or general isolation protocols, and are intended for single use to maintain hygiene standards.- Disposable Medical Surgical Gowns
Specifically tailored for surgical and invasive medical procedures, these gowns are constructed from high-performance SMS (Spunbond-Meltblown-Spunbond) non-woven fabric, which offers enhanced barrier properties against blood, bodily fluids, and microorganisms. They feature a reinforced design with a full-body coverage, including a high neckline, long sleeves with thumb loops to secure cuffs under gloves, and a robust tie closure at the back for a secure fit. The SMS material ensures breathability while maintaining a high level of liquid resistance, critical for prolonged wear during surgeries. Compliant with strict medical standards, they minimize the risk of cross-contamination between medical staff and patients in sterile operating environments.- Disposable Protective Suits
Designed for maximum protection in high-risk environments, these full-body suits provide comprehensive coverage from head to toe. Made from heavy-duty, impermeable materials such as laminated non-wovens or polyethylene, they are resistant to liquids, aerosols, and airborne particles. Featuring an integrated hood, elasticated wrists and ankles, and a front zipper with a storm flap for a complete seal, they prevent any direct contact with hazardous substances, infectious agents, or contaminants. They are widely used in biohazard labs, pandemic response scenarios, chemical handling, and other high-risk situations where full-body protection is imperative. Like all our disposable garments, they are single-use to ensure optimal safety and prevent cross-contamination after exposure.
Why Choose Us
1. Industry-Leading R&D and Technological Prowess
2. User-Centric Insight and Demand Translation
3. End-to-End Quality Excellence
4. Rapid Market Responsiveness and Innovation
5. Global Supply Chain and Delivery Reliability
6. Market-Proven Results
Reliable Quality Assurance: A Comprehensive Overview
Core Principles of Reliable Quality Assurance
Key Components of RQA Implementation
Benefits of Reliable Quality Assurance
Challenges in Implementing RQA
Core Principles of Thoughtful Service
Key Elements of Thoughtful Service Implementation
Benefits of Thoughtful Service
Challenges in Practicing Thoughtful Service
Let's learn about the locations where our products are applied.
We can provide samples within 7 days, as we usually keep them in stock. For mass production, the lead time is typically around 30-35 days
Normally, a 30% deposit is required in advance via T/T wire transfer, with the remaining 70% balance due before shipment. For more detailed inquiries, please contact your product specialist
The warranty is from 12-24 months, according to different models. Detailed info please contact with our product specialist
Thank you for your interest.
We specialize in high-performance indoor air quality solutions, and our product range includes:
-
Air Purifiers (portable, ceiling-mounted, wall-mounted, and commercial-grade models)
-
Ventilation Systems (fresh air systems with or without heat recovery)
-
Dehumidifiers and Humidifiers (for residential and commercial use)
-
Water Purifiers and Hot & Cold Water Dispensers
-
Replacement Filters and related accessories
We support OEM & ODM customization, and all products meet international certification standards (e.g. ETL, Energy Star, CE, CB).
If you’re looking for a specific solution, I’d be happy to recommend a suitable model for your market.
Best regards,
Yes, we fully support OEM, provide:
-
Custom logo printing & packaging design
-
Private label services
-
Customized product specifications (materials, sizes, contents)
-
Regulatory documentation support for your local market (CE/FDA/ISO, etc.)
Whether you need your own brand on masks, gowns, or test kits, or wish to develop a unique product line, we’re happy to support you from design to production.
Looking forward to learning more about your customization needs.
Best regards,